Concrete form plywood is an essential material in the construction industry, particularly in the creation of concrete structures. Its versatility, strength, and durability make it a preferred choice for formwork applications. However, to maximise its benefits and ensure a successful project, it is crucial to follow best practices when using concrete form plywood. This article outlines key considerations, tips, and techniques to enhance the effectiveness of concrete form plywood in construction.
Understanding Concrete Form Plywood
Concrete form plywood is specifically designed to withstand the rigours of concrete pouring. Unlike standard plywood, it is manufactured with a higher density and moisture resistance, allowing it to endure the weight and pressure of wet concrete. The surface of form plywood is treated to prevent adhesion with concrete, ensuring easy removal once the concrete has set. This characteristic not only facilitates a smoother de-moulding process but also helps maintain the integrity of the concrete surface, which is crucial for aesthetic and structural purposes.
Moreover, the longevity of concrete form plywood is a significant advantage for contractors. With proper care, it can be reused multiple times, making it a cost-effective solution for various construction projects. This reusability is particularly beneficial in large-scale developments where multiple pours are required, as it reduces waste and the overall environmental impact of the construction process.
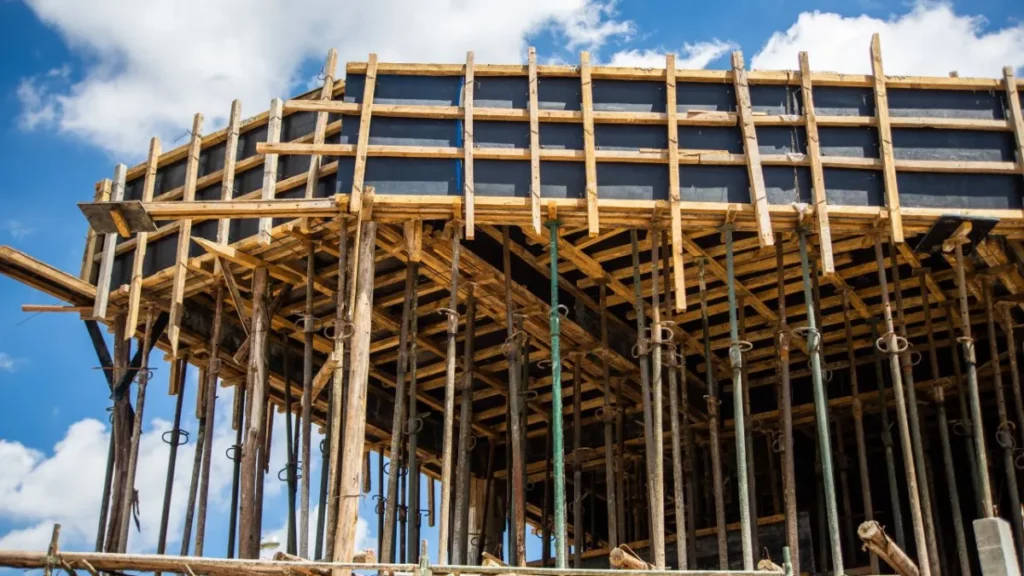
Types of Concrete Form Plywood
There are various types of concrete form plywood available, each suited to different applications. The most common types include:
- Film-Faced Plywood: This type features a plastic film overlay, providing a smooth finish and high durability. It is ideal for projects requiring a fine surface finish, such as architectural structures and decorative concrete elements. The film not only enhances the aesthetic quality of the finished product but also increases the lifespan of the plywood itself, making it a popular choice among builders.
- Structural Plywood: Made from high-quality veneer, this plywood is designed for load-bearing applications. It is commonly used in large-scale construction projects, including high-rise buildings and bridges, where strength and stability are paramount. The structural integrity of this plywood type ensures that it can handle the significant stresses associated with heavy concrete pours.
- Water-Resistant Plywood: This type is treated to resist moisture and is suitable for use in wet conditions, making it a practical choice for outdoor projects. Its water-resistant properties help to prevent warping and swelling, ensuring that the formwork remains stable and reliable throughout the curing process.
Key Features to Consider
When selecting concrete form plywood, consider the following features:
- Thickness: The thickness of the plywood affects its strength and load-bearing capacity. Thicker plywood can support more weight but may also be heavier and more expensive. It is essential to balance the thickness with the specific requirements of the project to ensure optimal performance.
- Grade: Plywood is graded based on its quality. Higher grades offer better surface finishes and fewer defects, which can impact the final appearance of the concrete. Selecting the appropriate grade is crucial for achieving the desired aesthetic and structural outcomes, particularly in visible areas.
- Moisture Resistance: Ensure that the plywood is adequately treated for moisture resistance, especially for projects exposed to the elements. This treatment not only prolongs the life of the plywood but also enhances the overall quality of the concrete, reducing the risk of surface imperfections and ensuring a more durable finish.

Preparation and Handling
Proper handling and preparation of concrete form plywood are vital to ensure its longevity and effectiveness. Incorrect handling can lead to damage, which may compromise the integrity of the formwork.
Storage Conditions
Store concrete form plywood in a dry, well-ventilated area, away from direct sunlight and moisture. This helps prevent warping and degradation. If possible, keep the plywood elevated off the ground to avoid contact with damp surfaces. Learn more about moisture at https://www.calibrecontrol.com/news-blog/2024/4/10/what-is-moisture-content
Inspection Before Use
Before using the plywood, inspect each sheet for defects such as cracks, splits, or delamination. Any damaged sheets should be replaced to maintain the quality of the formwork. Additionally, check for the presence of foreign materials, such as dirt or debris, which can affect the adhesion of the concrete.
Installation Techniques
Correct installation techniques are crucial for achieving optimal results with concrete form plywood. Following established practices can enhance the performance of the formwork and ensure a smooth concrete pour.
Securing the Plywood
When securing the plywood, use appropriate fasteners that are compatible with the material. Screws or nails should be driven in at an angle to ensure a tight fit. Avoid over-tightening, as this can cause the plywood to warp or crack.
Creating a Level Surface
It is essential to create a level surface for the formwork. Uneven surfaces can lead to inconsistent concrete pours and affect the structural integrity of the finished product. Use a spirit level to check for alignment and make adjustments as necessary before pouring the concrete.
Concrete Pouring and Curing
Once the formwork is in place, the next step is pouring the concrete. This process requires careful attention to detail to ensure a successful outcome.
Pouring Techniques
When pouring concrete, it is advisable to use a chute or pump to minimise the risk of damaging the formwork. Pour the concrete in layers, allowing each layer to settle before adding the next. This technique helps prevent air pockets and ensures a uniform mixture. To know more about mixture click here.
Curing the Concrete
Curing is a critical step in the concrete process, as it allows the material to gain strength and durability. Keep the concrete moist for at least seven days after pouring to ensure proper curing. This can be achieved by covering the surface with wet burlap or using curing compounds that retain moisture.
Removing the Formwork
Once the concrete has cured, the formwork can be removed. This process should be done with care to avoid damaging the newly set concrete.
Timing for Removal
Timing is crucial when it comes to removing the formwork. It is generally recommended to wait at least 24 to 48 hours after pouring before beginning removal. However, the specific timing may vary based on the type of concrete mix used and environmental conditions.
Techniques for Safe Removal
When removing the formwork, start at the edges and work your way inward. Use a pry bar or similar tool to gently loosen the plywood from the concrete. Avoid using excessive force, as this can cause the concrete to crack or chip.
Maintenance and Reusability
Concrete form plywood can be reused multiple times, making it a cost-effective option for construction projects. However, proper maintenance is essential to extend its lifespan.
Cleaning After Use
After removing the formwork, clean the plywood thoroughly to remove any concrete residue. Use a pressure washer or a stiff brush with water to scrub the surface. Ensure that all debris is removed before storing the plywood to prevent damage during storage.
Inspecting for Damage
Before reusing concrete form plywood, inspect it for any signs of wear or damage. Look for cracks, warping, or delamination that may affect its performance. Any compromised sheets should be repaired or replaced to maintain quality standards.
Environmental Considerations
As sustainability becomes increasingly important in construction, it is essential to consider the environmental impact of using concrete form plywood.
Choosing Sustainable Materials
Opt for plywood sourced from sustainably managed forests. Look for certifications such as the Forest Stewardship Council (FSC) label, which indicates that the wood has been harvested responsibly.
Recycling and Disposal
At the end of its life cycle, concrete form plywood should be disposed of responsibly. Many local recycling centres accept wood products, and some companies specialise in recycling construction materials. This not only reduces waste but also contributes to a more sustainable construction industry.
Conclusion
Utilising concrete form plywood effectively requires a combination of proper selection, handling, installation, and maintenance practices. By following the best practices outlined in this article, construction professionals can ensure that their projects achieve the desired results while maximising the lifespan of the materials used. Concrete form plywood remains a vital component in modern construction, and understanding how to use it effectively can lead to significant benefits in both quality and cost-efficiency.
In summary, the right approach to using concrete form plywood not only enhances the structural integrity of concrete projects but also promotes sustainability and responsible resource management in the construction industry. By prioritising best practices, builders can contribute to a more efficient and environmentally friendly future.
Other resources: Exploring the Advantages of F17 Plywood for Concrete Formwork